Durit Coatings was challenged to develop a solution that would increase the efficiency of injection molds by reducing the frequency of stoppages due to the wear and tear inherent in the industrial process. It is in this context that the PVD coating - Moldlub® - developed by Durit Coatings stands out as one of the main solutions to the injection molding industry's problem.
The challenge for the molding industry
In the design of an injection mold, there are several typical problems associated with it and, therefore, its correct sizing involves knowledge of plastic materials, materials used in the manufacture of molds, heat treatments, the complexity of plastic parts and the control of injection process variables.
The difficulty of demoulding, where it is important to minimize the extraction forces of the processed plastic parts, there is friction between the plastic part and the mould material. In turn, the shrinkage effect has a preponderant effect on the friction force generated between the molding surface and the injected article.
This way, the success of this phase is related to processing parameters, exit angles, finish, material properties at the extraction temperature, sizing of the extraction system and the coating of the molding surfaces.
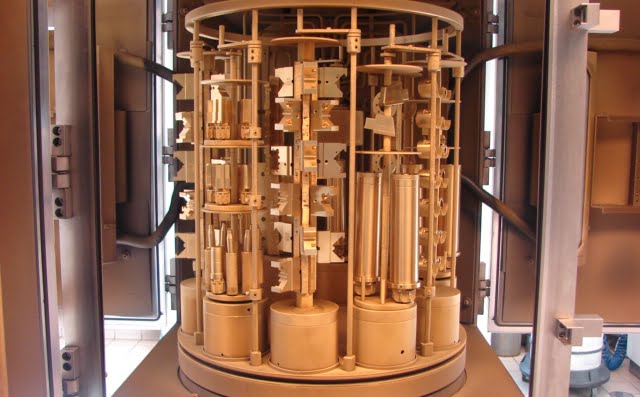
PVD - Coating process
The PVD process is an atomic deposition process in which a material is transformed into vapor from a solid source, transported and deposited on the surface of a substrate, offering greater resistance, durability and superior quality through an extremely thin and highly adherent coating.
Durit Coatings offers a wide range of solutions: HardSilK®; HardTiN®; DMold®; MoldLub®; ULTRA Impact® and also DLC's, DiExtra® and Diaplus®, to meet all these needs.
These coatings generally have a hardness greater than three times that of nitriding, a low coefficient of friction and are resistant to wear by adhesion and abrasion.
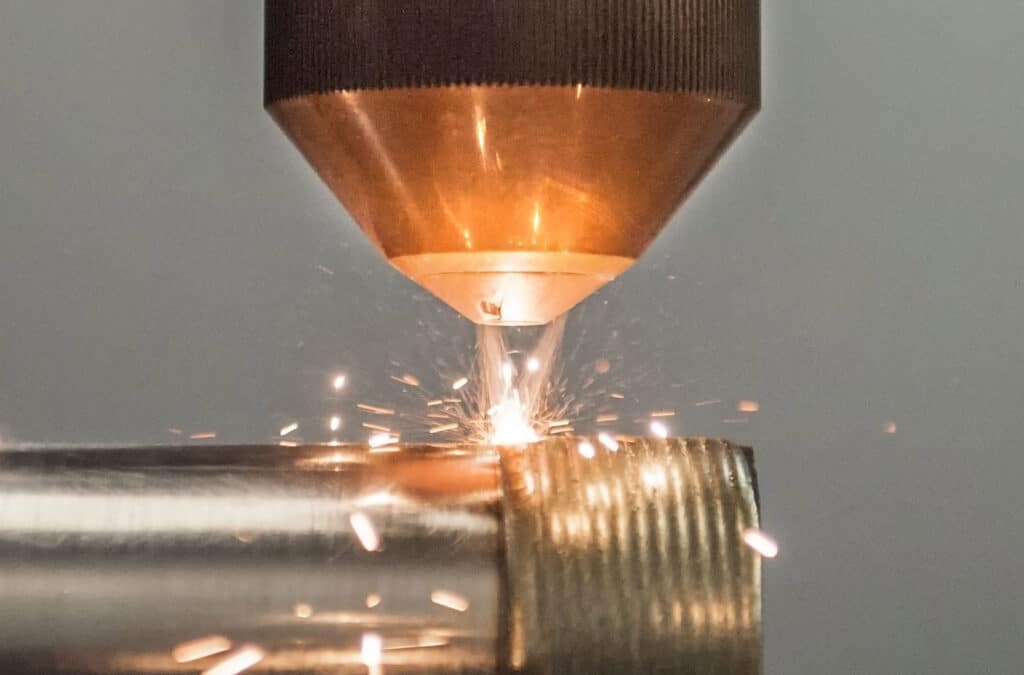
Laser Cladding - Surface improvement technology
Laser Cladding technology is used to improve the surface of molds and their recovery. It consists of depositing layers of material on the surface of components, but the added material, now in powder form, is injected against the surface of the component to be clad.
At the same time, a laser beam fuses this material and the surface of the part, forming a layer of material with a metallurgical bond to the substrate, which can be between 0.5 and tens of millimeters thick. It is therefore considered an additive manufacturing technique.
Laser Cladding technology is similar to conventional welding processes, but with the advantages of being able to build layers with controlled dilution, low heat addition, which results in a small thermally affected zone and low distortion of the components and zero or negligible porosity.
Through this process it is possible to deposit materials such as 1.2344 steel which, due to the high cooling speed of the process, has a hardness of 50-54 HRC after coating, without the need for heat treatment.
Vantagens das soluções PVD e Laser Cladding
One of the most notable advantages of applying this type of coating is the increase in wear resistance. However, some materials have an abrasive effect on the steel from which the mold is made. Materials such as fiber-reinforced plastics are the most critical cases.
Injection molding with percentages of between 30-70% glass fiber presents added challenges for the durability of the molding surfaces, especially when roughness is specified by polishing or texturing them. The severe abrasive wear caused during injection leads to frequent stoppages for mold maintenance.
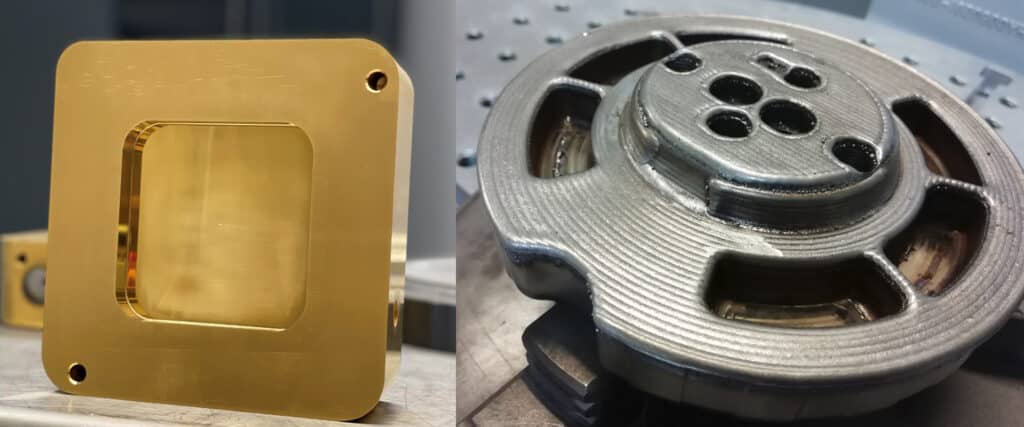
Advantages of PVD and Laser Cladding solutions
In response to this challenge, Durit Coatings has developed a PVD coating that is at the forefront as one of the main solutions to this problem in the injection molding industry: Moldlub®.
The MoldLub® solution has good wear resistance, acting as a "solid self-lubricant", a low coefficient of friction (reducing the extraction force by 300%) and high hardness (2000 HV), minimizing extraction problems in injected plastic components.
This improvement has resulted in a significant reduction in the extraction force of the processed part, both loaded and unloaded, faster filling of the plastic part, lower injection pressures, reduced roughness due to the PVD process and shorter molding cycle times.
This way, using this type of solution with coatings improves injection conditions and facilitates the extraction process.
Authors: Eng. Francisco Gonçalves and Eng. Marta Sousa (former Durit Coatings collaborator)